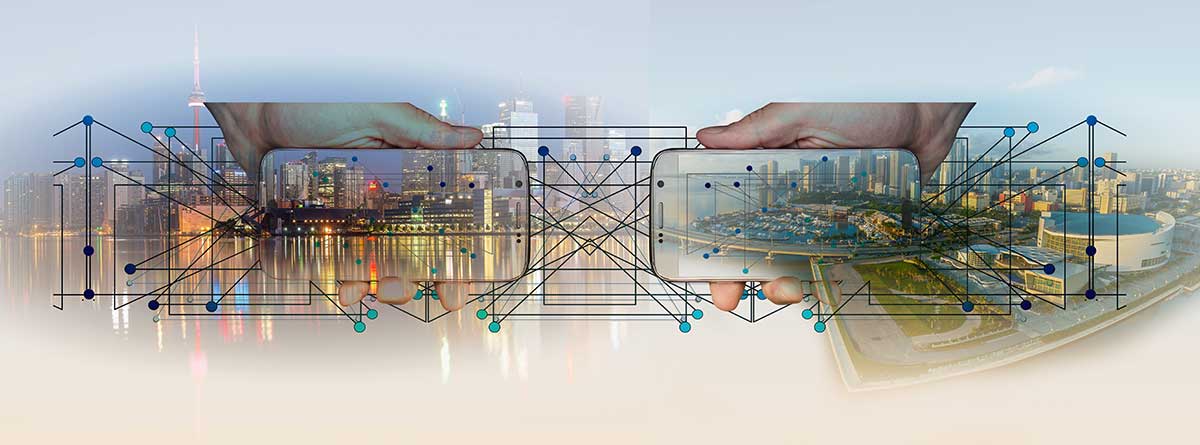
VALVE WORLD EXPO 2020: A journey to Data Utopia
Thanks to digitalization and industry 4.0, valve manufacturers can look forward to a promising future. A future with extremely decreasing defect rates, higher cost savings and most importantly improved competitiveness.
Digitalization and industry 4.0 have picked pace long ago. Many companies in the valves sector have already jumped onto the bandwagon enthusiastically. And while on it, they want to strengthen their competitiveness – with big impact and most importantly huge volumes of relevant data. This ride into the future is moving fast nearly all across the industry. Even though no one exactly knows what to expect from industry 4.0. But it seems promising and encouraging. Is there really a Utopia waiting out there?
Digital is better – and will come out on top. According to TÜV Nord Group, this express train zooming towards the future is unstoppable. “Digitalization is a key concept of the future of our economy and industry”. It is a trend just like globalisation or urbanisation, emphasises Christian Ziegler, Manager Marketing, Communication and Digitalization at SMC.
Increased revenues, decreased costs
The implementation has begun long ago. The large plant and engineering construction sector is working purposefully to leverage industry 4.0 “to increase revenues, shorten product development time and decrease costs,” explains Jürgen Nowicki, spokesperson for the Large Industrial Plant Manufacturers Group (AGAB) citing the 2017 study “Potenziale von Industrie 4.0 im Großanlagenbau” on industry 4.0 potential for the industrial plant engineering and construction sector that was conducted by the German association VDMA (“Verband Deutscher Maschinen- und Anlagenbau e.V.”) along with management consultants maexpartners.
72 per cent of the respondents in the study described the potential to increase revenues and profits through digital products and services as “very relevant” to them. 14 per cent of the participants in the survey, based on this optimism, expect an additional profit of over 10 percent in the coming five years. A perspective that could help resist the increasing competitive pressure from developing countries like China.
Real-time data processing
A development that the valve manufacturers will join, if they wish to keep up with the trend. Because in the future of manufacturing, "information technology will play a big role – not only in the operations and control of production plants but also in bringing together and analysing machine data or information on energy consumption,” forecasts Festo, provider of automation and control technology solutions. Real-time data collection and processing are becoming increasingly possible. New analysis options are getting created, for example for predictive maintenance or acquiring a holistic view of energy flows and consumption.
Integration is not limited to within one's own factory, but according to Festo, is increasingly supporting data transfer and data synchronisation with external systems. In the future, production sites, suppliers and customers will work increasingly closer with each other, predicts Festo. “To enable this, it is crucial to have standardised interfaces and data formats as well as high performance networks and connections”.
Increasing decentralised automation
Valve manufacturers are on the move. “In the past years, there has been a significant increase in decentralised automation of process valves, precisely in step with digital communication,” confirms Sebastian Kundel, Product Manager Automation Process Valves at Bürkert. The benefits that can be reaped in the design, planning and construction of plants are in the forefront. Decentralised Artificial Intelligence for the diagnosis and digital transfer of data have been relatively less implemented. In the meanwhile, technical possibilities and software features would become more self-evident. There is a critical shift of thinking in using status data beneficially, says Kundel. “A transparent view of plants, machines and production processes will be possible and enable new business models for operations, service and maintenance”.
Digitalization of control valves
According to Samson, to start with, sophisticated valves are fitted with position controllers. On the other hand, there are simple valves – for example On/Off valves – that are still equipped primarily with solenoid valves and/or limit switches. Their digitalization may not be that advanced, although Samson also offers solutions here too. “On the one hand the valves must pass on information to the entire system, and on the other hand they must be capable of receiving information from the system”. In case of Off/On valves, we are still a “long way” from reaching the high level of digitalization that we see in control valves.
Higher plant availability
Samson is absolutely convinced by digitalization too. It enables round the clock monitoring of valves. Directly ascertainable values like set point, actual value, control deviation and driving pressure can be recorded continuously and additional information can be added to these in the future.
The position controller notifies the user in advance of an error condition in and on the valve. Notifications like “internal leakage” or “actuator defect” require no further data interpretation by the user. Digitalization along with the valve diagnosis feature integrated within the position controller enables increased plant availability “as potential error conditions can be early detected and rectified”. According to Samson, the future goal is to completely avoid error conditions, which could be achieved with approaches like feed forward control and practical maintenance management.
Software equipped field devices
Significant drivers are the general rise in the automation level, plant availability and productivity along with high quality standards. In parallel, software equipped field devices have become the norm and many devices in the market now come with digitised operations. “The share of digitally automated process valves has strongly increased and has now reached a significant level”. With developments like the IO-link, a communication system used for connecting intelligent sensors and actuators to an automation system, the growth has not quite stopped. The definition of properties that are important for process technology in the specification, particularly with respect to functional safety, is still under way,” explains Sebastian Kundel.
Digitalization of control and switch-based valves, according to Bürkert, signifies decentralised plant design. The company is developing solutions. An example is the valves system with integrated position or process controllers and control heads in process valves. Only in this manner can process data, for example, on valve position and process dimensions and diagnosis data for functional safety and maintenance requirement, be made available continuously to the process through sensors and related analysis. And transferred in digital form from the field level to the master level.
Industry 4.0 as a philosophy
Digitalization and industry 4.0 surely influence customer products, in the sense that they must be ready for industry 4.0, but they also influence the internal processes of valve manufacturers. SMC illustrates this with the example of its paperless assembly operations. “Earlier we used to have printed drawings and instructions. But today our employees in assembly operations have a Tablet-PC from where they access the latest and up-to-date instructions and bills of materials. This reduces error rates and media breaks,” says Christian Ziegler, Digitalization Manager at SMC.