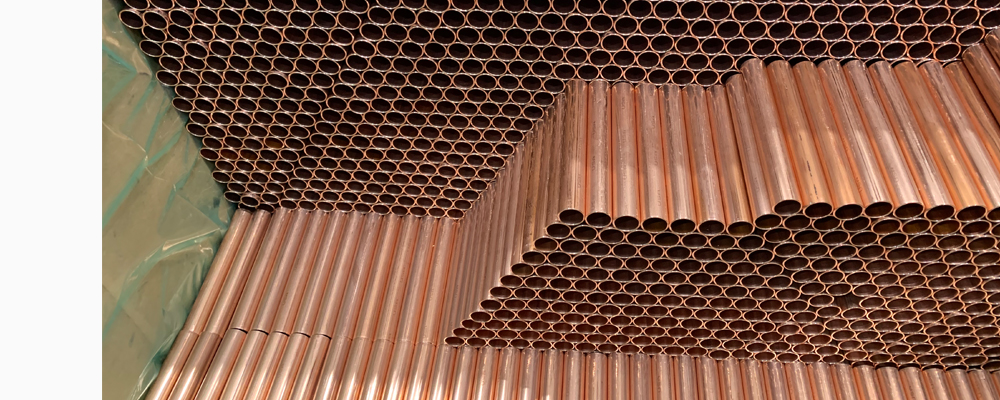
New developed machine (series 215/318) – delivered to the leading manufacturer of fitting systems in USA
After successful tests on the new developed machine series 215/318, based on the system of the proven chipless cutting line model 215, the first machine was now delivered to the US plant of the leading manufacturer of fitting systems. The development of the new series was based on the chipless cutting head and a new compact machine design with tube endworking and high-performance transport system. The material feeding system is designed for tube coils made from steel or copper or as an alternative, straight tubes. The coils can be loaded individually or stacked on a driven automatic turntable.
The connecting air-suspended guiding wheel between turntable and straightening section provides continuously adjustable chucking. The straightening section can be equipped with a compact quick-change device for the different tube diameters, allowing set-up times of less than one minute. The concentric, hydraulic gripper is operated by a dynamic servo axis and synchronized with the turntable. Both operations, the automatic defect detection and the automatic recognition of the tube fittings are integrated in a color recognition and positioning system.
The parts are cut chipless with rotating tools and minimum material waste with tool lifetime up to 150k cuts. The cut parts are transported by automatic grippers into and through the end working station. The length of the finished parts is measured and bad parts are automatically sorted out. Soft and hard copper qualities can be processed precisely without deformation of the tube ends. Continuous and precise machining prior to hydroforming and the benefit of minimum tooling cost provided by the new machine generation, all good reasons for the leading fittings manufacturer to order three more lines at Reika.